In the sci-fi series Star Trek, characters could use machines called replicators to instantly materialize just about any food, beverage, or tool on site. A more primitive version of the replicator has already emerged in our society. The formidable combination of scientists, engineers, and entrepreneurs are busily working to push additive manufacturing into our everyday reality.
Already scattered throughout our society are commercial desktop 3D printers, which are amongst the first few generations of additive manufacturing devices in the wild. Cost and material limitations present challenges for broad application, but as the technology advances it will drastically impact the way we make our physical goods. Changes in how we organize our economy and our cities are not too far downstream.
Champions of the technology claim the potential of greatly reduced environmental impacts through our consumer economy. Lower impact manufacturing techniques, addition of better properties to goods, and reduction of the replacement rate of all of our goods are among the benefits claimed.
In my last article, I discussed the urbanization of economic sectors and made mention of additive manufacturing. I try to be cognizant of environmental impacts of any technology that is entering the urban fold. Urban manufacturing and industrial zoning have poor environmental and health reputations, but new additive technologies could challenge that narrative.
Understanding additive manufacturing
As defined in the American Society for Testing and Materials (ASTM) International’s 2012 standard terminology for additive manufacturing technologies, additive manufacturing or AM is a process of joining materials to make objects from 3D model data, usually layer upon layer, as opposed to subtractive manufacturing methodologies that remove layers. The term broadly and commonly refers to a collection of 3D printing technologies that continues to develop.
Additive manufacturing emerged from innovations in computer, laser, and computer aided design(CAD) software technology. If we go by patents, 1986 was the year in which additive manufacturing came into being with Chales Hull’s depositing of the first patent for stereolithography or SLA.
SLA falls into the greater category of Vat photopolymerization. Today, researchers and entrepreneurs have expanded the number of categories of additive manufacturing to seven. As defined by the ASTM, these categories include..
- Binder jetting, in which a liquid bonding agent is selectively deposited to join powder materials.
- Directed energy deposition, in which focused thermal energy is used to fuse materials by melting as they are being deposited.
- Material extrusion, in which material is selectively dispensed through a nozzle or orifice.
- Material jetting, in which droplets of build material are selectively deposited.
- Powder bed fusion, in which thermal energy selectively fuses regions of a powder bed.
- Sheet lamination, in which sheets of material are bonded to form an object.
- Vat photopolymerization, in which liquid photopolymer in a vat is selectively cured by light-activated polymerization.
Capabilities
Additive manufacturing is fundamentally more flexible than conventional subtractive manufacturing technologies. Outside of dimension, material, and resolution, AM machines have little limitation to what they can print. This potential is controlled and bounded by software that instructs the AM hardware on how to construct objects. The combination of AM software and hardware allows for efficient small scale production and rapid distribution of 3D printable designs.
These capabilities have been taken advantage of during the current coronavirus crisis. Additive manufacturing-enabled companies and enthusiasts have developed and produced desperately needed components for medical equipment. In Italy, a partnership between Isinnova and Lonati, two local 3D-printer companies printed 100 values for around a dollar each that the original manufacturer sold for over $10,000 each.
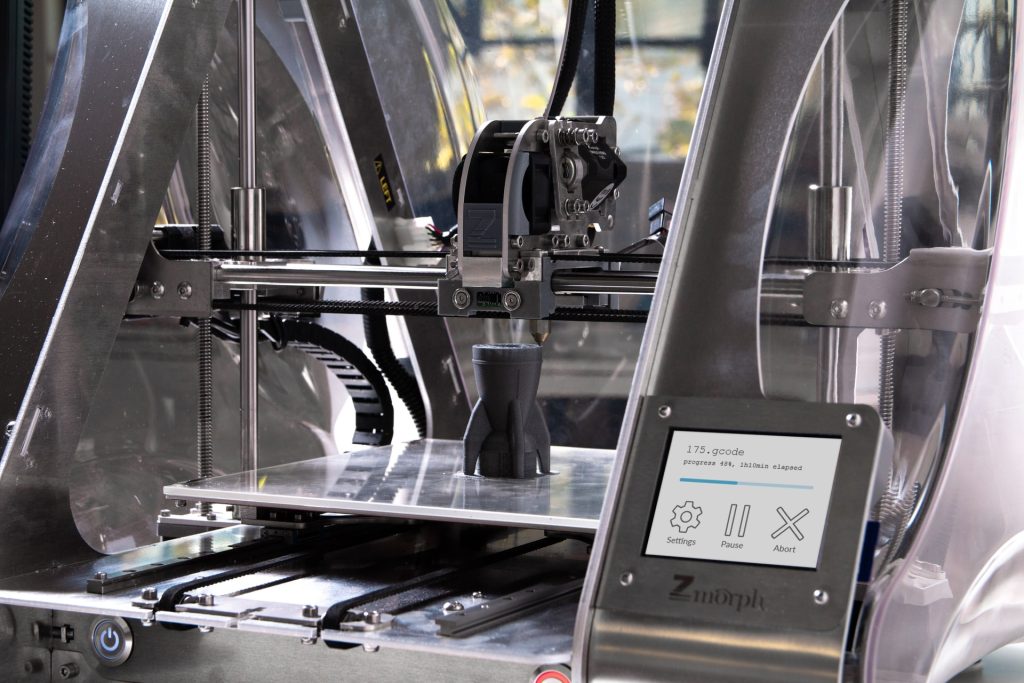
Additional AM boons come from building from the bottom up that allows for the formation of freefrom geometries that can imbue valuable properties into printed objects. These properties include shock absorption, impact control, built-in cooling, and vibration/noise dampening. More environmentally impactful properties that can be introduced into objects are lightweight design and low material usage.
Lightweight design is achieved through decreased density with complex hollow structures. Both can be a part of reducing the climate impact of manufacturing. A project done by Loughborough University and industry partners found weight reductions of up to 50% with optimal designs. This enables better fuel efficiency of vehicles, and reduced wear on transportation infrastructure.
Decreased raw material usage naturally accompanies lightweight design, reducing material costs like reduced weight reduces fuel costs. Environmental impacts from sourcing are reduced with decreased usage. Additionally, usages of materials like aluminium, titanium and nickel can be reduced, lowering the cost and impact on strategic reserves.
Aside from material and fuel savings, secondary effects of additive manufacturing further reduce environmental impact of the manufacturing industry. Rapid prototyping, access to spare parts, and decentralization of production and recycling are amongst the environmental positives that additive enables.
AM’s ability to efficiently produce at a small scale allows designers to produce prototypes at an unprecedented rate, and for consumers to easily print spare parts. Faster prototyping allows designers to be more thorough in a limited period of time, preventing errors that could lead to waste further down the line.
Waste is also reduced through an increased availability of spare parts. Spares and custom prints can drastically reduce the replacement rate, the rate at which goods are thrown out and replaced. Additive machines could viability produce the spare parts that many companies cannot.
Efficient small scale production with an AM machine can quickly produce parts or a potentially more complex piece for the quick extension of the service lives of many goods. Creative and individual use of AM hardware and software can also find opportunity to fix many damaged objects.
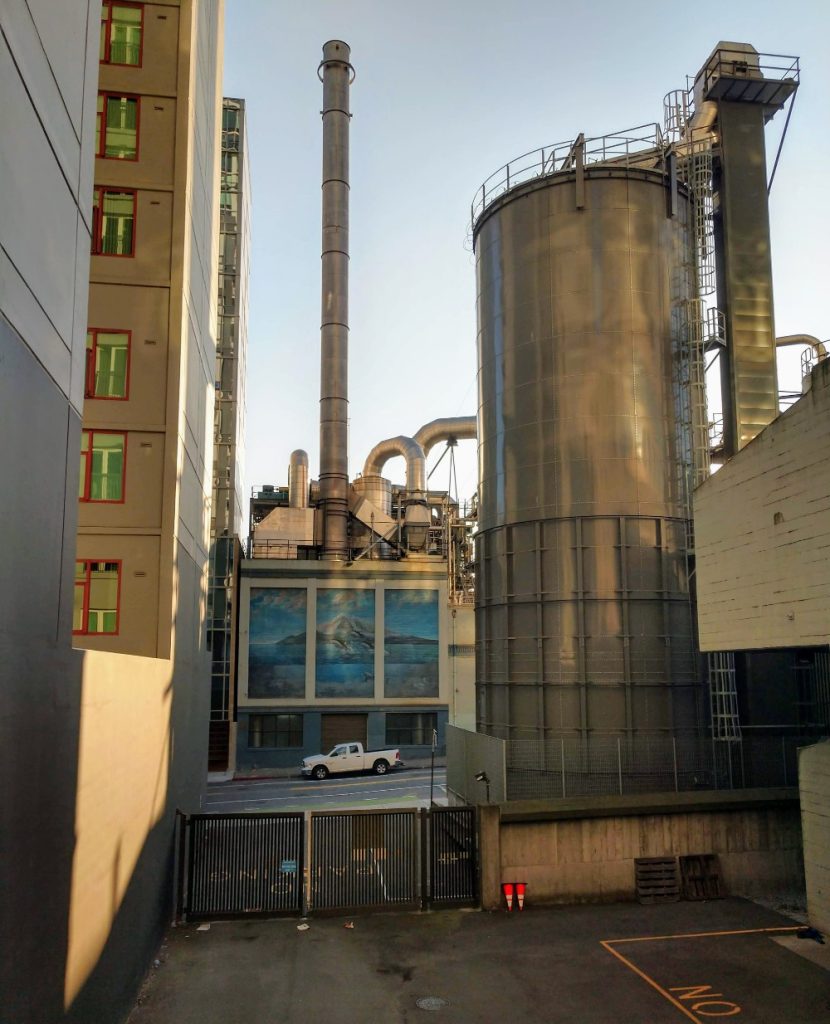
Viable small scale production allows for manufacturing to be much closer to the densest concentration of consumers: cities. Urban 3D printing factories have already popped up in cities like New York, and Shenzhen. Close proximity to dense populations has allowed for decreased transportation related environmental costs. Close urban proximity also deserves greater scrutiny and regulation of the potential environmental effects of the technology may have.
Major Environmental Concerns
Manufacturing and industry leaves a major environmental footprint. According to the EPA, the sector made up 22% of the United States’ greenhouse gas emissions in 2017 and continues to pollute our air, soil, and water. Challenges posed by current manufacturing techniques originate in the energy and material requirements that additive manufacturing will also require.
Energy intensiveness is a shared challenge for many urbanizing technologies. Fortunately, this energy is required in the form of electricity that can be produced in a low impact manner. Energy usage of 3D printers can be reduced with scale. Downtime between prints requires more energy usage per output than nonstop printing because of start up and shut down energy usage.
Raw material impact concerns are present for AM. Plastics and metals are the main inputs for AM processes. Sourcing and processing costs will always be a concern. All materials used in AM have an innately high level of embodied energy due to the process’s consumption of highly processed and refined materials.
Traditionally, recycling acts as a mitigating force to material environmental impact. Current understanding of AM processes indicates that recyclability of additively manufactured products may be worse than conventionally produced goods. Recyclability will vary across the seven families, as each one uses different chemical processes.
SLA transforms raw material, which may make non recyclable products. AM processes degrade a percentage of powders and photopolymers, up to 30% of material used in powder bed fusion may degrade. Fill materials, powders and fibers etc., are difficult to separate from the plastic matrix creating a high barrier to recyclability of the base material.
Another obstacle to economic recycling could include components that are printed with multiple materials, making it difficult to separate into usable material. Structurally, the current recycling infrastructure may not be able to process components with properties that are only endowed during AM processes.
Altogether, poor recyclability gives AM a poor end of life score in a life cycle assessment (LCA). It also worsens the print phase of the AM life cycle because prints often require an outer support structure that is used to preserve the structural integrity of the intended object during the print. LCA woes continue into the use phase for AM created objects.
Studies have indicated that toxicity of prints may be a problem for Material Extrusion(ME) and VAT photopolymerization. A study out of UC Riverside used zebrafish to access the toxicity of 3D printed parts. The researchers found that zebrafish embryos exposed to fused deposition modeling(FDM), a type of ME, and SLA printed parts had reduced survival rates, reduced hatching rates, and higher rates of deformities, compared to the control group. SLA-printed parts had much higher rates of negative indicators.
Additional health concerns have arisen from detected particulate matter, nanoparticle, volatile organic particle (VOC), and pollutant emissions. These emissions are generated during printing material preparation, the printing process, the removal of parts, the post-processing hase, and the utilisation phase. While not fully understood, many of the AM families release dust particles, flue gases, and vapors that are harmful to health.
A report by the German EPA-equivalent, the Umweltbundesamt put together a graphic on the assumed emissions from 3D printing processes.
Conventional manufacturing methods and their factories also produce particulate emissions, but they are subject to environmental regulations. The decentralization that AM allows may allow individuals to evade those regulations, which is becoming more pressing when AM printers are located within cities. One notable absence from the potential list of emissions/waste products from AM is wastewater, a significant product of conventional manufacturing.
Proliferation of commercial desktop 3D printers has granted amateurs access to potentially polluting and toxic technologies. Intermittent usage of commercial printers by amateurs is energy intensive. Amateurs also produce more misprints and waste, are not responsible for sufficient cleanup and disposal, and are currently not subject to any environmental standards.
Today and Tomorrow
Desktop 3D printers are already in the homes of enthusiasts, workshops, and academic facilities. The proliferation and success of the commercial desktop 3D printer market is certainly a testament to how far additive manufacturing has come. The market demonstrates the demand for the technology and the need for close attention to usage of personal 3D printers.
However, we’re reaching a turning point where the growth of AM for production-type use cases begins to rapidly outpace the growth of recreational use cases. In the 2019 Wholers report, the consulting group highlighted a decline of the number of desktop AM system manufacturers and an increase of industrial AM system manufacturers.
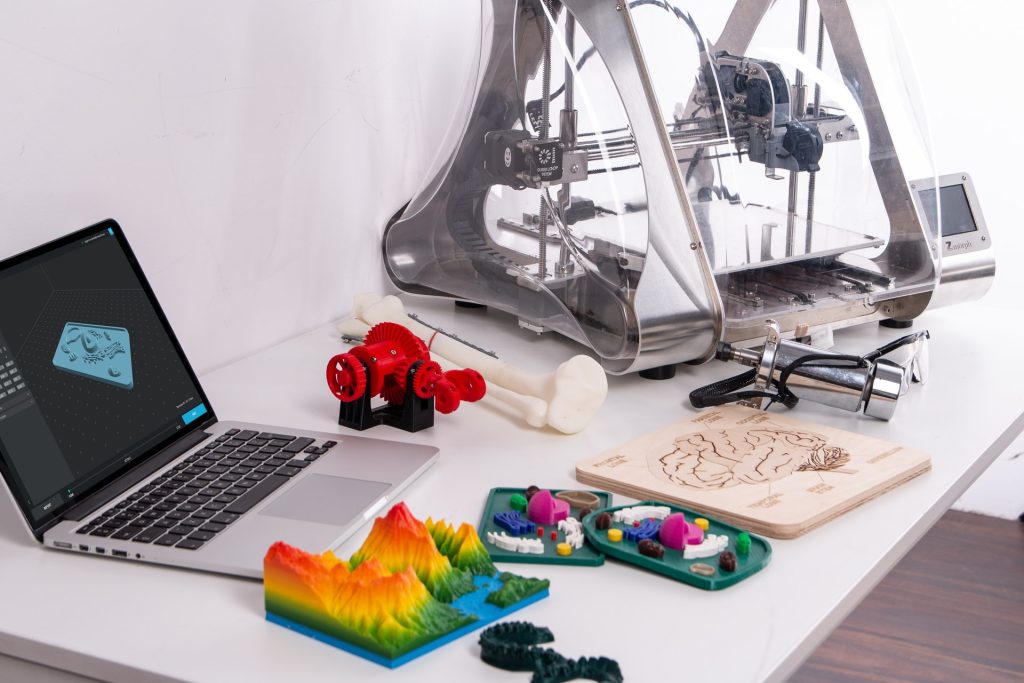
The explosive growth of industrial use and the significant decline of personal use is an indication that additive manufacturing is starting to mature as a technology. Projections of where the technology will by the end of the decade see integration of AM into existing manufacturing workflows. The assumption is that integration will be enabled by improvements to printing speed, energy efficiency, computing power, and post-processing automation through the 2020s.
Applications developed from those improvements have created a trend in the projections to begin to push AM technologies into the mainstream of medium and large scale production. Though that prediction may be a fit bold, as 2019 worldwide revenue of AM machines and services had just broken into the tens of billions of dollars. Worldwide manufacturing is a tens of trillions dollar market, so AM still has a ways to go.
Additive manufacturing may not have to operate at medium and large scale production to achieve the efficiencies needed to achieve a competitive price point. Viability of small scale production allows for decentralization of production and mass customization.
An expansion of applicable materials from just metals and plastics is also among the forecasts for AM’s future. Ceramics, cements, and organics are among the material feedstocks being developed for AM use. Bioprinting as an application of AM to print tissues for consumption and testing already occurs on smaller scales, substituting animal cruel practices.
To address the pollution and toxicity concerns of the AM process, industry expects advancements in post-processing treatment and print process to increase the safety of AM. The EPA has been studying the emissions released from 3D printing, so we’ll hopefully have AM-specific policy in the near future to check emissions. Recyclability seems like it will remain a challenge for additively manufactured objects. Research thus far is inconclusive on a feasible and realistic way to close the loop on AM.
Takeaways for cities and urbanists
Additive manufacturing is already in our cities, but for the most part it exists in a small education and recreational manner. While I’m wary of amateur use of additive tools, future standardized AM facilities may be able to mitigate the technology’s emissions and yield the benefits that AM promises.
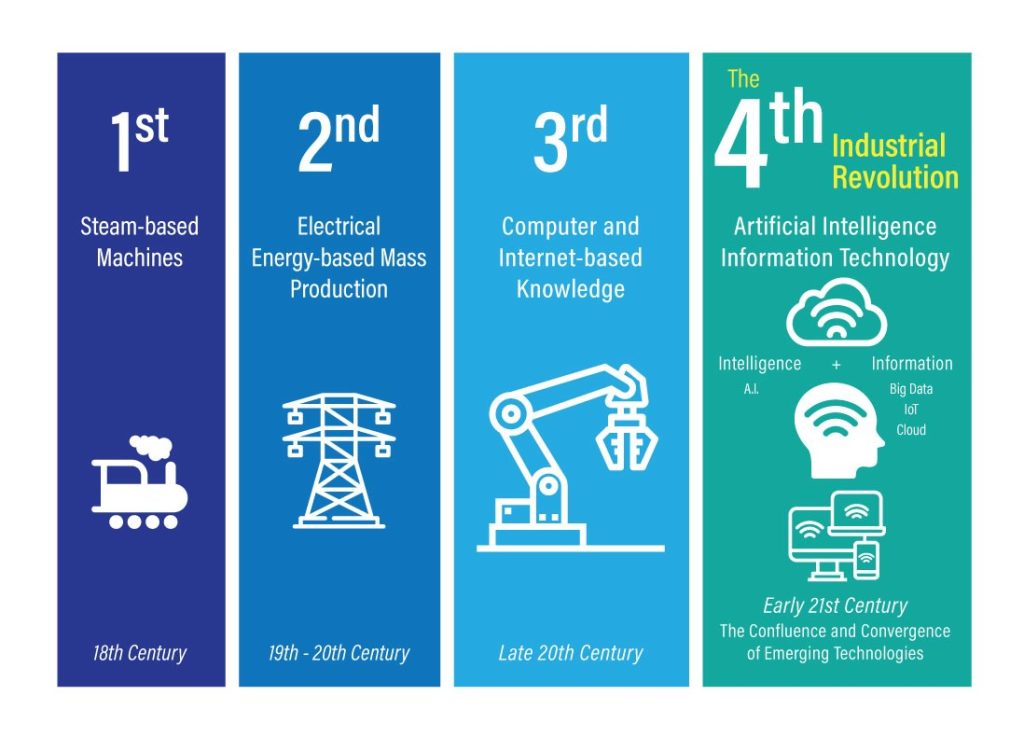
Like automation, AM is one of the horsemen of the Fourth Industrial Revolution, the encroaching technological and economic revolution. For many experts, the explosion and disruption of the technology’s physical footprint looks to be inevitable. How the technology affects our communities and their respective environmental footprints is up to policymakers.
I’m not sure what the most environmentally optimal distribution of AM looks like, but some models do stand out to me. Hyper-localization of AM facilities is one of those models, it would minimize transportation costs, take advantages for efficient small scale production, and be accessible to as many people as possible. Demand that allows for continuous printing would also need to exist for energy efficiency, but proper planning should take care of that.
As additive manufacturing matures, planners and policymakers should take notice of the difference between AM and conventional manufacturing and adjust land use policy accordingly. We’re used to manufacturing facilities at require scale to operate, AM does not. Where AM facilities will be allowed to be built will influence how much they can impact the carbon footprint of our economy and people.
Overall, I am optimistic about the future of additive manufacturing and want to see it reduce the carbon footprint of society. AM deserves the attention of urbanists because it’s already in our cities, growing in footprint, and has environmental and health consequences. Industrial zones do not have a good reputation in urban life, maybe AM will change that.
Shaun Kuo is a junior editor at The Urbanist and a recent graduate from the UW Tacoma Master of Arts in Community Planning. He is a urban planner at the Puget Sound Regional Council and a Seattle native that has lived in Wallingford, Northgate, and Lake Forest Park. He enjoys exploring the city by bus and foot.